If you’re a company that stores fuels and lubricants in steel storage tanks that are exposed to the elements, tank under floor corrosion is a major risk. How do you overcome such a fundamental force of nature?
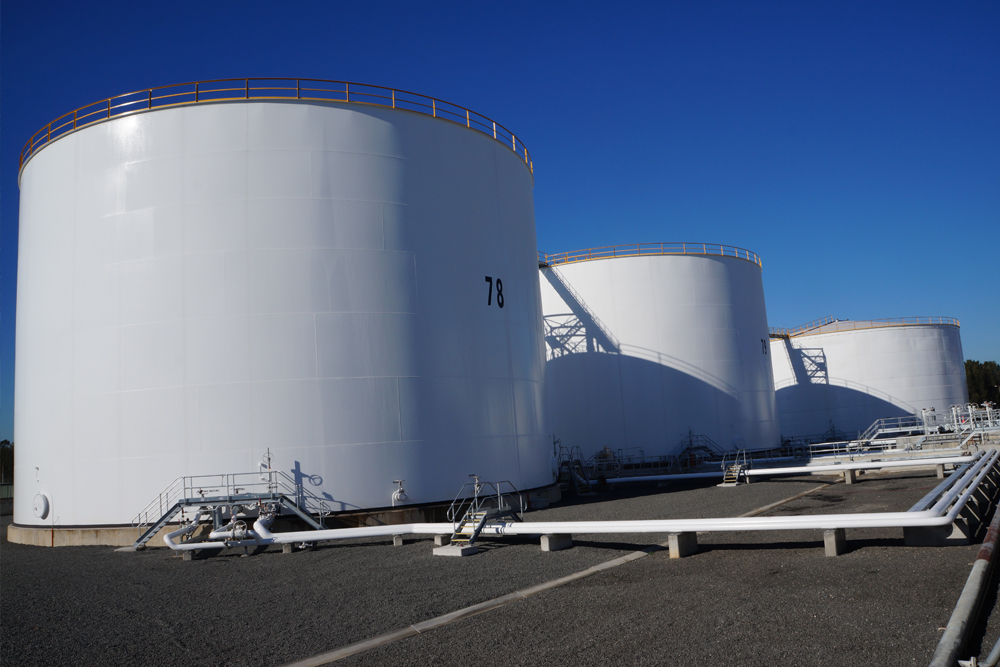
Viva Energy has developed a Risk Based Inspection (RBI) tool to determine how much time can elapse before a tank needs to be removed from service for an internal inspection. The RBI factors in a wide range of data, including the rate of corrosion. The problem is, when water gets under the tank floor, actual corrosion can occur at a different rate than the predicted.
The invisible problem
In the early 2000’s, high underfloor corrosion rates resulted in tanks being taken offline after only seven years which was earlier than the target service interval of ten years. This was to prevent a leak through the tank floor. Subsequently the associated inspection and repair costs were higher because the corrosion damage was widespread and required extensive repairs. This then leads to the storage tank being out of service for extended periods of time which adds further cost to the business.
Michael Stanic, Viva Energy’s Tank Reliability Engineer explains why underfloor corrosion was happening: “The joint between the tank and the plinth is sealed using a flexible silicon sealant. Due to tank movement and deterioration of the sealant over time, the sealant separates and cracks. This situation allows water to enter the underfloor area.”
Solved by local expertise
Luckily we had our Reliability and Integrity Manager, Tony Toko, looking at the problem. He came up with the idea of the weather strip.
“The weather strip design was developed back in 2008,” Tony explains. “It was an engineering solution to basically eliminate water getting under our tank floors. I came up with the idea of affixing a flat piece of metal onto the projection plate of our vertical storage tanks. It helps water flow away from the bottom of the tank, and means that maintaining the plinth seal isn’t as critical as it used to be.”
Simply stunning results
It’s a simple solution that’s had a massive impact. “We’ve found that by putting this weather strip on, we effectively stop water from getting in underneath the tank,” says Michael. With a weather strip installed you reduce underfloor corrosion which then means the service interval can be extended safely to a new target of fifteen years – this is double the service interval to previously not having a weather strip installed. This is a great outcome considering our average age for storage tanks is 55 years. For new tank builds the first service interval before an internal inspection is required can now be extended to 30 years, which is incredible.”
A safe future
Putting the weather strip in place initially presented its own challenges, as Tony remembers. “The original weather strip was attached using an epoxy glue. Exposure to the sun and rain resulted in the strip peeling off. There was a bit of trial and error in the early days, until we found a design that can withstand the weather and conditions and adopted the current design which involves welding on the weather strip to the projection plate.”
Today, all new tanks are constructed with the weather strip in place and it is also retrofitted to existing operational tanks when it is practical to do so. Eventually all Viva Energy’s vertical storage tanks will be protected by the weather strip. In fact, it’s appearing on tanks around the world. Shell, who licenses its products in Australia through Viva Energy, adopted the weather strip design and have rolled the design out globally which is a great recognition for our talented local team.
It’s even been adopted by other companies in the industry, which doesn’t bother Tony. “It’s a small industry and the word gets around. If the weather strip makes more storage tanks safer, as well as protecting the environment, then that’s a good thing! We’re happy to share our innovation.”
Learn more about our tank maintenance and compliance with the Australian Standards for Safe Storage and Handling of Fuel.