Managing the conversion of a 90 year old refinery into a large scale storage and import terminal takes team work and resilience. All the while continuing to supply about a quarter of New South Wales fuel needs. With extensive engineering and operational experience, Clyde Conversion Manager Julie Seymour, was the ideal person to manage this enormous undertaking.
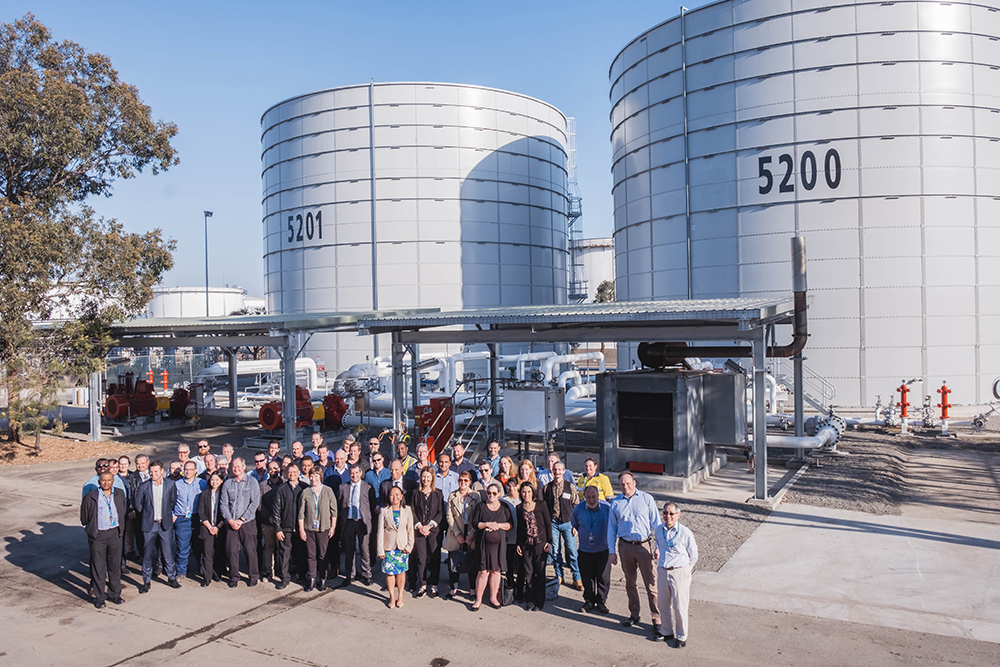
Refinery to Import Terminal
The facility at Clyde operated as a refinery from 1928 to 2012 when the decision was taken to cease refining in NSW. Decommissioning the plant and obtaining planning approvals took a few more years, with work to convert the old refinery site into a large scale import terminal commencing in earnest in 2015.
The brief for the project sounded deceptively simple … “Convert the Clyde Refinery into an Import Terminal”. However, our Clyde facilities help supply around a third of New South Wales’ fuel needs including a significant volume of jet fuel to Sydney Airport. With the terminal being such a critical part of NSW’s fuel supply, shutting it down even temporarily, to enable demolition and construction works was never an option. Julie and her team were tasked with ensuring that 24/7 operations continued without impact to our customers for the duration of the conversion project.
The close to four year project, which will soon draw to a close, has involved demolishing the refinery processing units and ancillary assets, and consolidating the remaining infrastructure into a smaller area. As a large scale import terminal, Clyde is set to enjoy a number of newly constructed assets including new fuel storage tanks, fire systems, high voltage electrical transformers and switch rooms. In addition, the refurbishment of existing assets into new configurations better suited to terminal operations has necessitated major works (or ‘turnarounds’) on 11 tanks, the installation of new valve manifolds, and the installation of kilometres of new pipework involving over 750 pipework connections.
Three of the largest refinery tanks that were historically used to store crude oil have been completely refurbished and had new geodesic domes installed to enable the storage of Jet A1 for supply to Sydney Airport. These investments have facilitated improvements to our process safety and environmental performance, ensuring Clyde Terminal continues to operate safely and efficiently into the future.
Demolition Challenges
Managing a large-scale demolition and construction project on a major hazard facility adds an additional layer of complexity to managing safety at the work site. This was particularly the case when planning how to demolish five chimney stacks that were part of the old refinery complex, and had been a well-recognised part of the Parramatta skyline since the early 1960s. Despite sounding somewhat unusual for an operating fuel terminal, simultaneous controlled explosive demolition was determined to be the safest way to bring the stacks down.
After six months of preparation and liaison with Department of Planning, EPA and Safework NSW, approval was granted to proceed with the demolition plan. Liberty Industrial, who was engaged to manage the demolition project, meticulously set the explosive charges and brought four of the five stacks down within seconds of each other, precisely and as planned. However one stack stubbornly refused to fall. It turns out the recalcitrant stack was built with far more steel reinforcement than its construction drawings from the 1960s had indicated – it had been really built to last! Despite the setback, the demolition team remained committed to bringing the stack down safely. After a series of smaller charges were detonated, the stubborn fifth stack accepted its fate and toppled down safely on its expected fall path. The outline of the chimney stacks on the Western Sydney skyline was no more.
The demolition challenges also included a redundant 70 metre pipe bridge over Duck River that needed to be removed without impact to the adjacent mangroves. With tidal movements only allowing a window of a few hours to execute the work, the bridge was lifted from its supports, turned 90 degrees by a mobile crane mounted on a barge, and floated down the Duck River to the Clyde wharf. This was a project that due to its complexity, meticulous planning and execution saw Liberty Industrial winning a World Demolition Award in 2016.
The project team was also determined to minimise the environmental impact from the refinery demolition, with the majority of the 38,000 tonnes of scrap metal being recycled. In addition, 30,000 tonnes of clean high grade sand recovered from the redundant LPG storage facility was transported from site and reused in building projects in the greater Sydney region.
“It’s about people working with people”
Julie’s extensive engineering and operational experience meant that being the Project Manager for the conversion of the Clyde Terminal was a natural fit. Over the many years of construction and demolition, there have been approximately 50 Viva Energy team members involved in the project managing over 200 contractors. Being such an old site, as work progressed, the team often encountered challenging legacy issues and, in this environment, focusing on the safe execution of work had to be the overriding priority.
Central to the success of the project has been Julie’s team. “I’m proud to be surrounded by people who care deeply about safety, and the quality of the project they’re delivering for the organisation.
“The team’s strength comes from its diversity and maturity, and the camaraderie that develops after working together for so many years. We had people join us from all disciplines, from different backgrounds and with a broad range of experience. We’ve learnt from each other, and this has meant we’ve been able to get creative with our solutions and deliver the project safely.”
“It’s also important to keep a sense of humour – not everything goes the way you anticipate. The old assets have surprised us with a few unexpected challenges and there’s definitely been moments of frustration, but we try not to let small set-backs impact us. In a project of this scale, spanning multiple years, it’s been important to recognise what we are delivering and achieving along the way.”
“We’ve also worked closely with our Supply and Operations teams to make sure the project doesn’t make their jobs more complicated than necessary, and to minimise any potential impact on our customers. It’s about people working with people, understanding what needs to be done and finding solutions that work for everyone – including our customers.”
Find out more about our Clyde Terminal here or visit the Sydney Living Museum to learn about its history.