Truck Loading Gantry Operator John Begg explains how a key innovation in our Omega system has transformed multiple orders for bulk fuel customers and carriers.
Our bulk fuel delivery service is a big part of our business at Viva Energy. Every day across Australia, we supply customers large and small with the fuel products they need, wherever they need them.
Now, we’ve made this often complex logistical process smarter, safer and more efficient through improvements to the loading gantry systems at our refinery and terminals, enabling our customers to load multiple orders at the same bay.
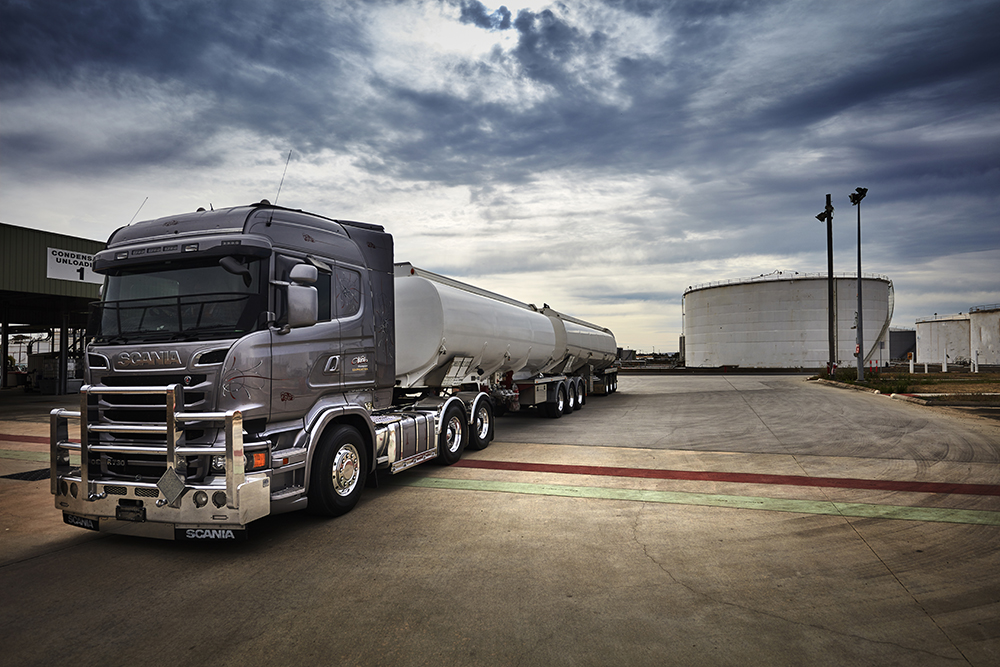
Called ‘Close Load at Bay’, this new functionality was introduced at our Geelong Distribution Gantry last year as an upgrade to the Omega system that manages our loading bay operations. It has since been rolled out to Viva Energy fuel terminals across the country.
“What we’ve got now with Omega is safer and a lot more flexible for our bulk pick up customers and carriers,” says John, who worked closely on the development and roll out of the feature. “It makes things a lot easier for them.”
Previously, the system lacked the ability to recognise when a fuel compartment had already been filled. “It was the reason why we wouldn’t allow customers to do multiple orders at once,” says John.
Specifically, if a driver tried filling multiple orders in a single run there was the risk of reconnecting the gantry arm to a fuel compartment that had already been loaded – leading to a potential overfill, spill, or mixing of products within compartments.
The new functionality of ‘Close Load at Bay’ however recognises when a compartment has been loaded, and ‘locks’ it to prevent such issues.
“Now, if the driver mistakenly pushes that compartment again, it just won’t allow him to load it.”
To load multiple orders, drivers can now simply disconnect from the gantry, and reconnect without leaving the bay. Omega then prompts them if they’d like to continue, or start a new load.
“In the past,” he continues, “to complete multiple orders, drivers would put it all on their own open order. They’d fill up, pull out and park in a parking bay, tag off and get their paperwork, go off to do the deliveries, then come back and load up again.”
“Now, they can have an individual order number for each customer, which makes it easier for them to manage customer orders. It’s a much faster, more flexible, and simpler process, and reduces the carrier’s costs by allowing them to utilise their loads a lot more effectively than they used to.”
And we believe we’re helping lead the way with the Omega system’s Close Load at Bay function.
“If multiple orders were to be loaded without a system like this in place, apart from it being very time consuming – loading, driving out, tagging off, going back into the bay and loading again – I believe it’s a method for something to go wrong,” says John.
“What we’ve got is safer,” he continues. “Plus, if the volume is available, customers can come in when it suits them to pick up an open order – they don’t have to submit details to the Order Fulfilment Team to have the load scheduled.”
And what’s more, John says, drivers and customers really like it. “They’re all very happy with this change. It’s a really good concept that has clearly improved our customer offer, and it’s working very, very well.”
Interested in learning more about Viva Energy’s bulk fuel solutions?
Visit our Transport Services page