It takes dozens of people working across a wide variety of trades to keep the Geelong Refinery well maintained and running smoothly. Key to that is clear and up to date communication on priorities and status of work. With large volumes of maintenance jobs required within the refinery covering multiple operational, trade and technical groups, understanding the status of activities in real-time is challenging but necessary to ensure safe and efficient outcomes. Now, thanks to a huge team effort, we have an innovative solution: LiveSchedule.
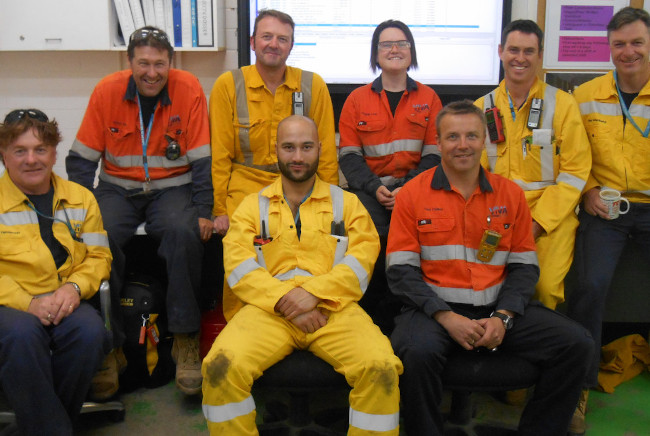
LiveSchedule is Viva Energy’s new digital maintenance communication tool for the Instrument and Electrical (I&E) Department. It allows anyone at the refinery to check the status of I&E maintenance activities in real time, and promotes the utilisation of maintenance resources in a more efficient and agile way.
Identifying the problem
Through engaging with our employees we found that there were inefficiencies around our maintenance execution. Working on the front-line, our I&E maintenance team was ideally positioned to identify the issues and also work on a solution. Through an intensive, design thinking training program, the team were empowered to lead the process, engage other stakeholders and define the challenges through a process of discovery.
The findings
All key stakeholders involved in maintenance at the refinery experienced similar frustrations that impacted their ability to work efficiently.
This included not always knowing what the day’s highest priority jobs were or when priorities had changed. They didn’t always know if there was a delay with a job that they had spent time preparing for. And they didn’t always feel confident that they could perform their work without being interrupted by people chasing job status updates.
A better solution was definitely needed!
Brainstorming
Supported by our Geelong Refinery Innovation Lead, Matt Hudson, the I&E team identified that a new way was needed to allow stakeholders to communicate in real time. “The team found that the lack of transparency in the status of scheduled maintenance activities was creating inefficient work practices,” says Matt. “Streamlining communication would enable resources to be allocated appropriately and expediently, deliver accurate status updates, reduce equipment downtime and ultimately increase efficiency and reliability outcomes.”
The refinery uses a proprietary software platform to manage its maintenance planning and while this together with the Enterprise Resource Planning (ERP) systems met most of our requirements, what was lacking was a communication tool that would support real time optimisation of the large volume of work being performed in a dynamic way.
Through a series of idea generation exercises that involved all stakeholders, the team came up with several potential solutions. From these, the concept of LiveSchedule was chosen as the option that would deliver the biggest positive impact on maintenance efficiency.
Let the experiments begin!
The process that ultimately delivered LiveSchedule was based on trial, feedback and refinement. This meant constantly updating the system and accommodating regular changes easily and cost effectively into the testing.
The team started by conceptualising what the LiveSchedule interface might look like on a whiteboard. Multiple iterations were trialed, with consideration for how information would be loaded, where it would come from and how it would be used.
From the whiteboard we moved to an Excel trial that supported additional functionality. We wanted to know if the trades groups would use a digital interface to update the status of their jobs. Over time we added some basic programming that not only displayed different jobs but also ranked them by priority.
The trials proved successful. “Tradespeople began using the system and getting value from it in all the ways we’d hoped,” says Matt. “Phone calls had reduced, our I&E team better understood work priority and schedule changes, and there was far greater transparency around works in progress.”
From idea to innovation
“The beauty of LiveSchedule is that it extends the capability of our existing maintenance scheduling and ERP platforms,” Matt explains. “It integrates seamlessly to enhance the display and provide an integrated communications solution.”
LiveSchedule has already had an enormously positive impact. Without the need to constantly provide job status updates, our tradespeople can work uninterrupted. It provides improved understanding of priorities and gives our I&E team flexibility to optimise their workflow to achieve a more efficient outcome. We have also eliminated duplication of personnel on jobs.
Overall we estimate an efficiency gain across our maintenance activities of more than five man-hours per day, or 1,300 hours per year, and this is just the beginning. LiveSchedule was launched to a test group of 20 tradespeople, supervisors and co-ordinators. Our vision is to roll out LiveSchedule to a further 30 personnel this year, which will improve engagement, efficiency and reliability outcomes even further.
We’re proud of the work of our I&E team in initiating and implementing this solution – which was the result of a Leadership Development training program with our partner G2 Innovation – a program which we were delighted to be named as a finalist for recently in the Australian Institute of Training and Development awards. This initiative also helped secure Viva Energy the title of 5th Most Innovative Company in the Australian Financial Review’s Top 10 ‘Most Innovative Companies’ for 2019 in the ‘Manufacturing and Consumer Goods’ category.
Learn more about Viva Energy’s Geelong Refinery
Find out more