Viva Energy Australia has customers in all the major industries. Within the mining, aviation, marine, transport, and oil and gas industries, they all rely on high-quality fuel for their safe and productive day-to-day business operations.
As Fuels Product Quality Lead, Sue Smith is part of the highly skilled, experienced and dedicated team that ensures Viva Energy fuel surpasses customer expectations from the refinery to the customer fuel tank.
To maintain this reputation and ensure the consistent high quality of our products, our Product Quality team are required to regularly requalify as Testing Officers. Through independent testing skills assessments and knowledge tests, our experts ensure they’re able to keep on top of evolving product knowledge and ensure their skills in product sampling and testing is current.
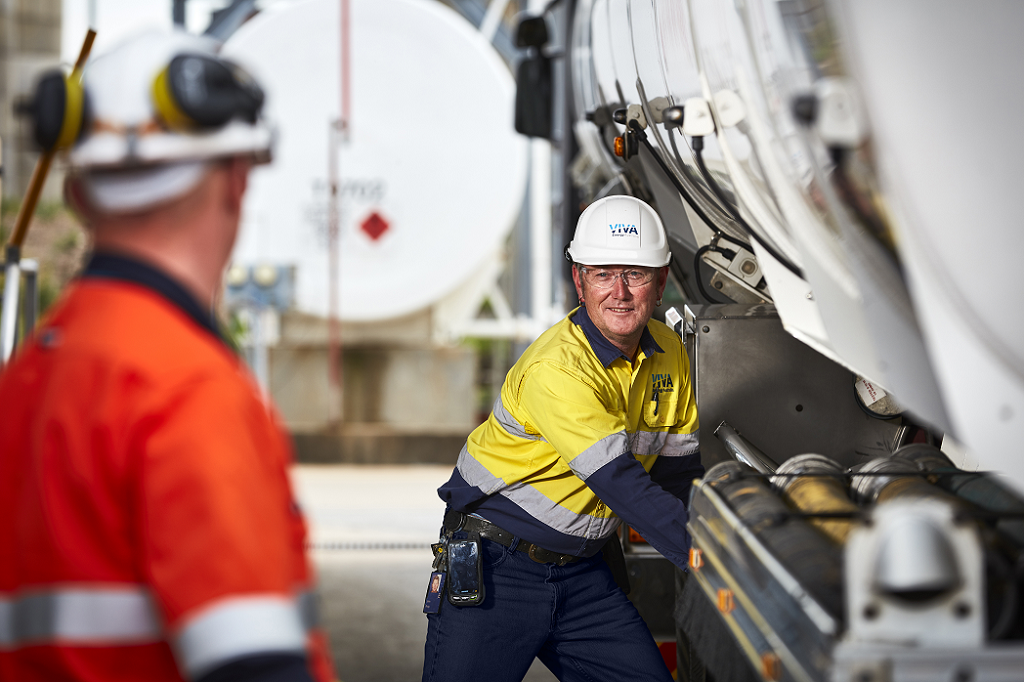
The framework for quality assurance
Viva Energy’s comprehensive Product Quality Assurance Framework is like a jigsaw puzzle of neatly fitting processes, procedures and documents that ensures there are appropriate quality checks at every stage of the Viva Energy supply chain.
This Quality Framework includes:
- Detailed fuel specifications to achieve compliance with legislative standards, management of fuel performance characteristics and ensuring fit-for-purpose fuel reaches the Australian market;
- Highly trained testing officers whose skills are assessed to ensure all fuel testing complies with internationally recognised standards;
- Best-practice sampling and testing for various fuels, including ground fuels, aviation fuels, marine fuels, and gas and biofuels, as they travel through the supply chain. To ensure that only the highest-quality, cleanest product is distributed to our customers.
The Product Quality (PQ) team oversees the execution of every aspect of this framework with quality control for the manufacture and at every stage of the supply chain up to the point fuel is transferred to the customer fuel tank.
The first point in the quality framework is when fuel is made. At this point ‘full specification testing’ occurs involving between 20 to 30 tests depending on the fuel. After manufacture, the framework establishes a complex range of tests at each step in the supply chain to make sure that a batch of fuel’s quality does not change.
Viva Energy looks at parameters like appearance and density as a minimum and then flash point, particle content, water content, colour, distillation as well as other characteristics to ensure the integrity of the product has not changed.
Meeting diverse standards
Different fuels are required to meet different standards. Aviation fuel has international requirements while diesel and motor gasoline need to meet national standards including regulatory obligations like cleanliness and operability requirements defined by Viva Energy to guarantee correct function of equipment or vehicle engines.
An example of the vehicle operability parameters are seasonal changes to fuel composition so that engines work faultlessly regardless of climate. For diesel fuel, cloud point is monitored monthly to prevent wax crystal growth that blocks filters or stops fuel pumps.
For petrol, vapour pressure is adjusted monthly so that fuel Is volatile enough in winter to ignite when a spark plug is fired but not so volatile that it results in vapour lock when temperatures increase in summer. This means Viva Energy ensures its customers’ vehicles operate in cold weather as well as warm.
Australia is divided into 13 recognised climatic regions and this makes supply of seasonally on grade fuel a challenge for the Viva Energy Supply Operations team who coordinate the flow of product around the country.
“When we start moving product down the supply chain – from a refinery tank into a ship, or from a tank into a pipeline to another terminal or another ship – we use what we call a ‘Product Quality System of Checklists’,” Sue says.
“For each product these checklists define what test is done on what sample and how often and where each sample is taken. Any variation of test results from the expected result defined on the refinery certificate is immediately referred to the PQ team to review and assess. All product is assessed critically and approved at each point in the supply chain.
“The operational staff at our Viva Energy terminals, our Testing Officers, are trained in product testing techniques with the expectation that all results obtained in our terminal laboratories are directly comparable to refinery laboratory results. All Testing Officers are required to pass a rigorous skill assessment, by an independent laboratory organisation and must demonstrate a high level of skill in conducting these tests. At all times, they are backed up by on call support from the Product Quality team whenever they need it.”
Exhaustive processes to achieve quality
Viva Energy has high fuel quality standards in compliance with the Fuel Quality Standards Act and tight operability parameters. However, where customers have specialist quality needs or more stringent requirements, the PQ team implements more rigorous specifications and fuel quality checking to ensure the customers fuel requirements are met.
“The fuel requirements for some of our large mining customers are very specific, so Viva Energy has to assess each batch supplied on their behalf and instigate controls and practices that ensure customer satisfaction,” Sue says.
“Viva Energy also has field support engineers for our major customers, where they come along and assist the user with storage, handling and fuel management to help them make the best use of the quality fuel they receive.”
Although the quality of Viva Energy fuel is Sue’s top priority, she says most customers just want to know they can get on with business as usual without unexpected disruptions. “It’s our job to make sure they have a seamless experience with our fuel. They just turn the key and the engine starts” Sue says.
Interested in Viva Energy's fuel products?
Find out more