How you store and handle your lubricant is a significant contributor to the performance and reliability of your equipment. Rob Cavicchiolo, Viva Energy Australia's Technical Hub Manager, gives his five top tips for safe lube handling.
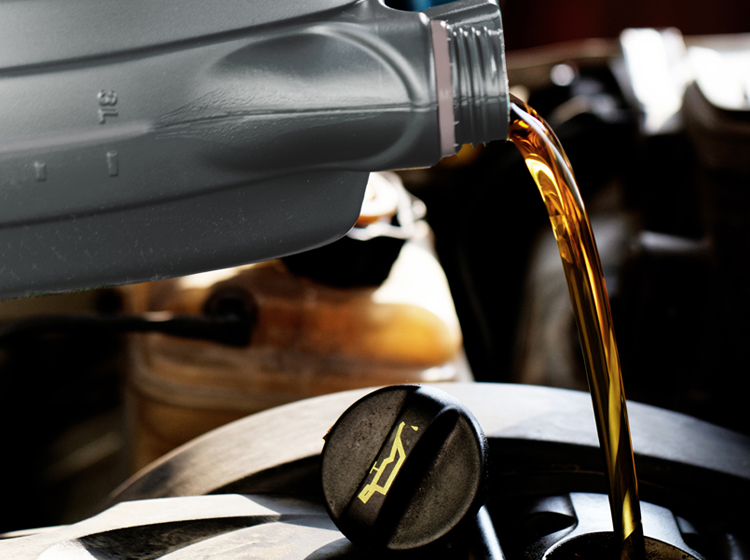
Avoid contamination during the dispensing process
For best performance, your lubricant must be clean and free of contaminants at all times. If you use a dispensing method that exposes the lube to the elements, such as a funnel and open vessel to transport it to its end use, you run the risk of having it become contaminated before the point of fill into your equipment.
It’s also important to ensure correct labelling of dispensing equipment, such as product names and colour coding, to avoid the risk of cross contamination between different fluids. Additionally, make sure you use only dispensers of an appropriate size, and ensure they don’t have lids left open (both oil and greases).
Moisture ingress is another source of contamination of stored lubricants. Drums have the ability to breathe and will ingress moisture, especially when left out in the open or when water settles on the top of the drum. One solution is to fit desiccant breathers to the lubricant storage system in use, to remove moisture from the air and prevent water from contaminating the lubricant. Wherever possible, store drums on their side with the bungs at nine and three o’clock, and under cover.
The right container makes a difference
In an environment where regular access to lubricants is required and sufficient quantities are used, it’s worth considering using an intermediate bulk container (IBC) instead of drums, which can be linked up to pumping equipment that delivers the lubricant directly to the application. This makes it easier to dispense the lubricant, and reduces the possibility of product contamination and wastage, as well as manual handling injuries.
Label your lubes
Sites often have many different type of lubricants used for multiple applications in their storage areas, such as gear oils, hydraulic oils and compressor oils. These all have different properties and technical characteristics, and if the wrong lubricant is dispensed for an application, you risk harming your equipment.
Each storage container should be identified and labelled clearly with the name of the lubricant it contains. Make sure you have good stock-rotation practices on site (i.e. first in first out) to ensure that lubricants do not end up being stored for long periods of time, and that existing older drums are used before newly ordered drums.
End-to-end colour coding is another option. Allocate a colour to your storage container, the corresponding dispensing equipment and the point of fill into the equipment, to ensure you avoid the mistake of mixing a gearbox with a hydraulic oil, for instance.
Dispense lubricants using the appropriate transfer equipment
Reduce manual handling tasks by incorporating the appropriate pumps and transfer equipment. This will not only help to minimise injuries, but also assist with keeping lubricants clean and reducing contamination before filling equipment.
Regularly inspect the transfer equipment for dirt, wear or damage. Clean them after use and keep them free of dust and grime.
Know your oils are still good oils
Routine condition monitoring of oils kept in bulk storage is good practice, to ensure that the lubricant is still within specification and has not been contaminated by water ingress, dirt or other lubricants.
This ensures that your equipment reliability has the best start with clean and on spec lubricants. Viva Energy provides comprehensive laboratory analysis for lubricants, and can help you ensure that best practice in storage and dispensing of your lubes is maintained, to avoid contaminants affecting the reliability of your equipment.
Want to know more about how to store and handle lubricants safely? Feel free to contact our technical helpdesk on 1300 134 205 or
email us here