Like all manufacturing businesses, Viva Energy generates waste from production, maintenance and other activities. To minimise impact to the environment, we’re committed to continually improving the effectiveness of our waste management programs.
Waste management can be broken into two components. First, waste can be eliminated, reduced, reused or recycled. Waste products can also be treated and turned into products that can be used by other industries or diverted through other appropriate channels.
We’re always on the lookout for ways to improve both components of waste management and in recent years, we’ve introduced two special initiatives.
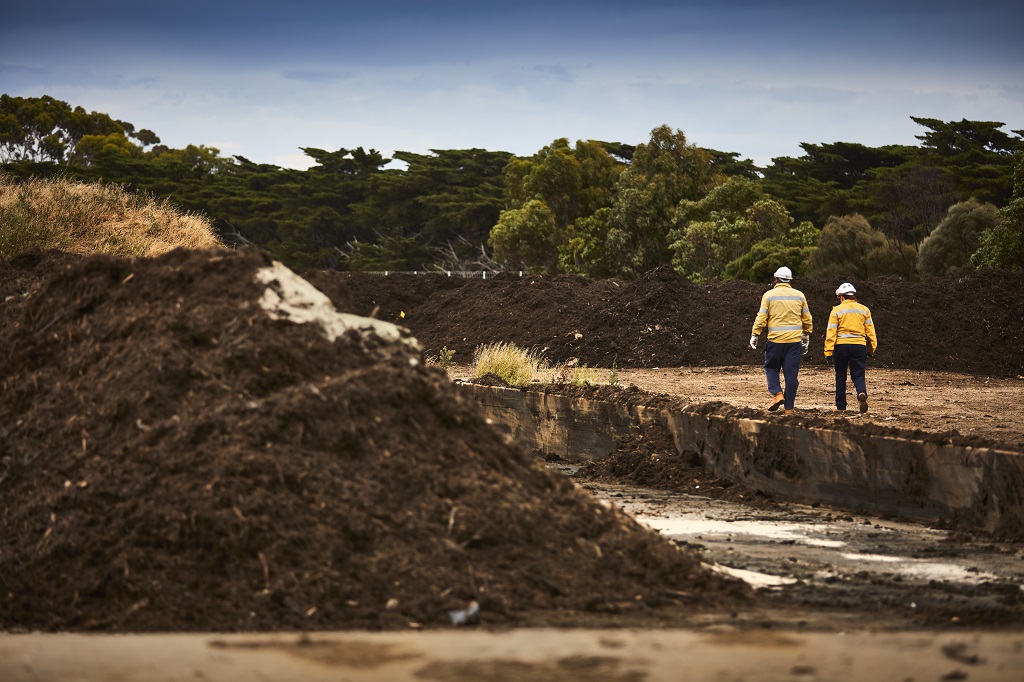
Nerita Gardens waste transfer station
In 2013, a rubbish heap at the Geelong Refinery was transformed into a waste transfer station, says Colin Davis, Environment Operations Lead at Viva Energy.
The waste transfer station has processed more than 2,400 tonnes of waste in the past two years, reducing landfill and conserving energy. As waste arrives at the station, it’s sorted and stored until it can be dealt with in the most efficient, effective and environmentally conscious way.
Soil from excavations, scrap steel, empty used drums, used pallets and scrap timber, waste concrete, asphalt and more arrive at the waste transfer station for processing.
“The concrete can be crushed and used on-site as a hardstand or used off-site,” Colin says. “The pallets are collected and then taken away, similar to a bottle refund scheme. Empty drums are inspected and either re-used or crushed and recycled as scrap steel. Timber is stockpiled and then we hire a chipper or send it off-site to be chipped and used as mulch.”
Steel, copper and other more valuable material is either collected or sold to third parties, depending on market conditions. Spent catalysts containing precious metals are sometimes sold to specialists who will extract the metals, and other times used in cement kilns to help with that process.
Shoe Park: Creating compost from waste
Over at the Shoe Park facility, hydrocarbon sludge waste is composted and transformed into soil conditioner mulch – in just 12 to 14 weeks. That mulch has so far fed more than 100,000 native trees, mostly located in Viva Energy’s buffer zones and parklands surrounding the facilities.
The waste would otherwise end up in a specialist landfill area since untreated hydrocarbon waste takes a long time to break down.
Dawn Conway, Geelong Refinery Environment Lead, says the waste comes in as a wet hydrocarbon sludge.
“We treat the sludge waste in geo-bags where water is removed by seeping through a specially designed membrane,” Dawn says. “Then the sludge characteristics are analysed to ensure they meet certain environmental criteria.”
The next step involves something that comes from our very own backyards. Green organics sourced from local government through the waste we put in green bins are used as a bulking agent. The dewatered hydrocarbon sludge is mixed with this bulking agent in predetermined ratios and formed into batches.
“We sometimes add other nutrients to create the correct blend where required,” Dawn says.
Once the sludge and bulking agent are mixed, the composting /bioremediation process begins through complex biological activity (bugs). Enhancement of the composting process means the ‘good bugs’ do their work and consume the hydrocarbon waste, converting the material into a mulch and soil conditioner.
There is constant monitoring of the process to ensure its effectiveness. “We test and record the temperature, moisture and pH on an ongoing basis to assess the biological health of the batch and make decisions on things like turning of the batches and adding water,” Dawn says.
Once the process is complete all material is then tested to approve it for its next role as a soil conditioner.
These and other initiatives mean Viva Energy continues to minimise the impact to the environment with thoughtful waste management processes.
To find out more about Viva Energy’s Geelong Refinery
Click Here